Operations Management. Strategy, Process design and supply.
Operations management for products & services. Achieving performance via strategies, process design & supply chain.
4.20 (41 reviews)
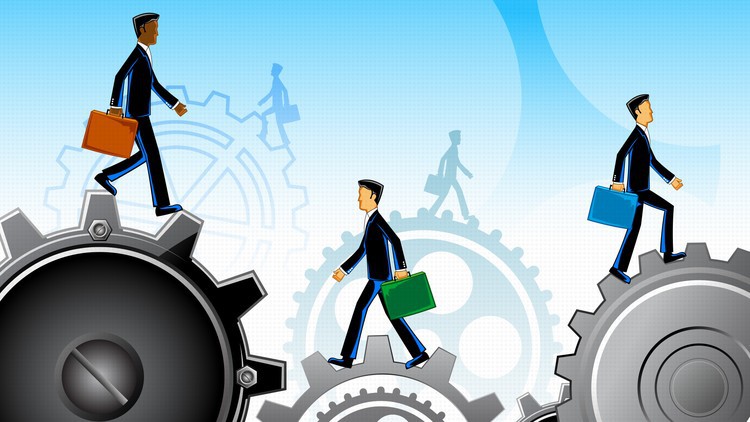
211
students
7.5 hours
content
Jul 2024
last update
$69.99
regular price
What you will learn
What operations management is.
Primary and secondary functions of an organization.
The differentiation between a product and a service.
The Characteristics of an operation
What the Triple bottom line means to an organization
Operation management indicators.
Stake holder expectations.
Understand the five key performance indicators quality, speed, dependability, flexibility and cost.
Understand what a strategy is.
Understand how strategies are created, how can ops management support or create a strategy.
Learn about order winning and order qualification characteristics of a product or process.
What is the product lifecycle and how it impacts strategies.
Learn about flow metrics of cycle time, Takt time, lead time, Work in progress & utilization via exercises.
Understand process design in the context of standardization and environment.
How process design is impacted by the volume and variety of product.
Understand how process mapping and process chart can help to improve and develop a process.
How process layout can be created and how it is correlated to the volume and variety of product to be made.
Line balancing. How to ensure that a process is ran as efficiently as possible.
How human resource management can help and aid operations management.
Learn how to design a job through Scientific management. Method Study, work measurement, work sampling and Time study will be understood through worked examples
Understand how important ergonomics and environment is in relation to job design.
Understand how job design has developed to include motivation theory which includes the behavioral approach.
Learn how to deliver product to the customer via operations scheduling. Understand the principles of loading, sequencing, scheduling and monitoring and control.
How to manage capacity in operations management. Which includes Long, medium and short term planning.
Understand capacity planning measurement of Utilization and overall equipment effectiveness.
Understand different types of capacity planning. Level demand, Chase demand or manage it.
Why is inventory important, what is it, cycle counts and the positives and the negatives of inventory.
The cost of inventory, Economic Order quantity, managing inventory, the bin system, the ABC system, measuring inventory and inventory management systems.
Understand what supply chain management is and perform exercises on how to choose a supplier.
Material requirements planning (MRP), Manufacturing resources planning (MRP II), Enterprise resource planning (ERP). Bill of Materials (BOM).
Screenshots
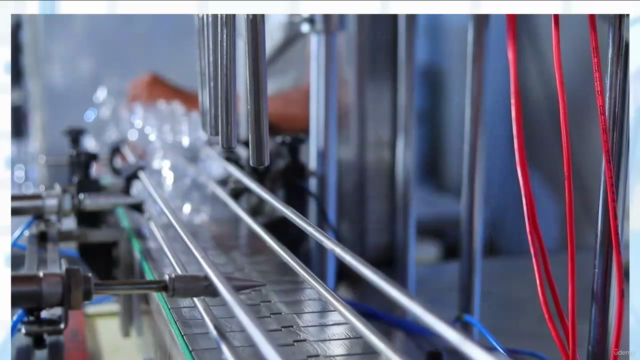
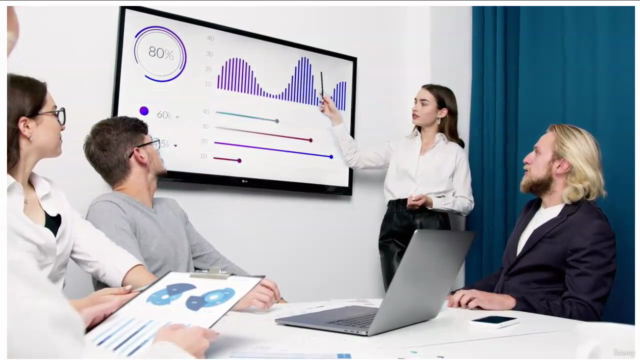
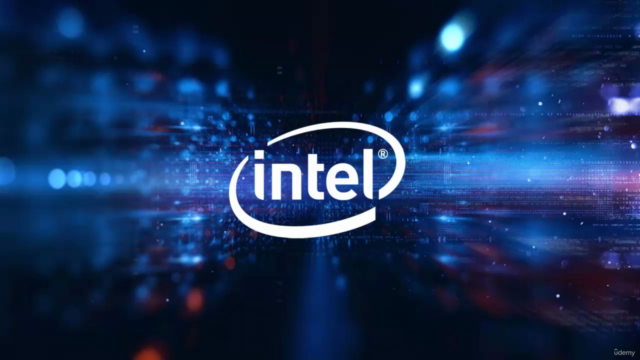
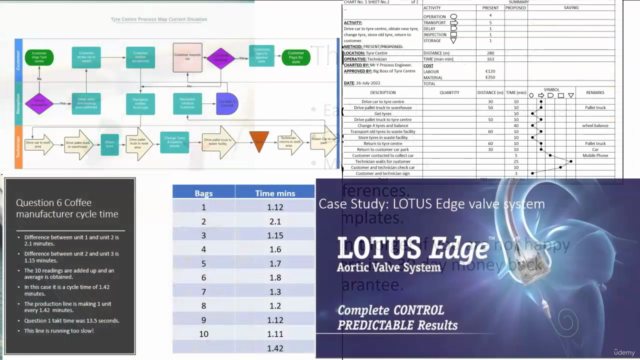
Related Topics
4381422
udemy ID
11/4/2021
course created date
12/23/2022
course indexed date
Bot
course submited by